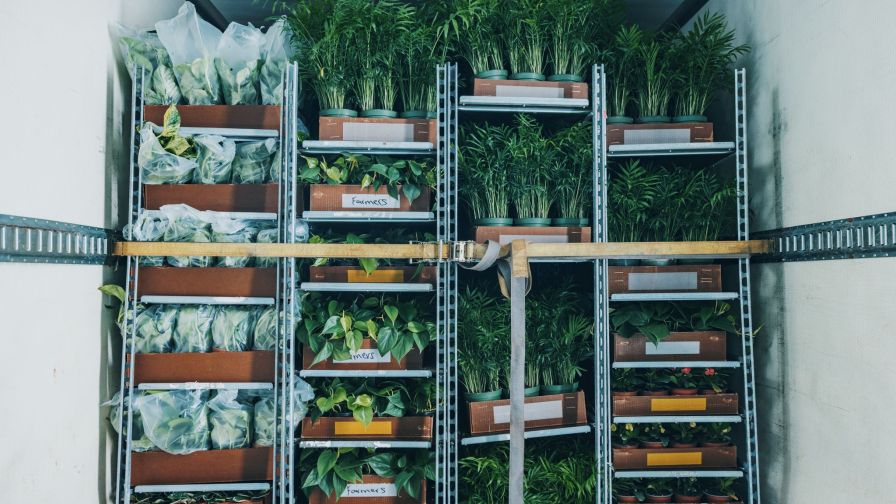
These plants are all tucked in on a reefer trailer so they stay warm until they arrive at their destination. | Container Centralen Inc.
All plants are cold-sensitive to one degree or another, and young plants even more so. But shipping poinsettias to a Minneapolis big-box store in December requires special consideration. We talked to a few folks who do it all the time to gain their insights about shipping cold-sensitive plants during the winter months.
Before delving into specifics, it’s worth mentioning that everyone emphasized the importance of clear communication with all those involved, from growers to carriers and the customers at the other end. Don’t assume the truck driver or the loading dock personnel understand how damaging even a few minutes of cold exposure can be. Talk with them and help them understand the issue.
As Joyce Opulgencia, Buyer and Greenhouse Manager at Emma’s Garden Growers, told us, “It’s critical that everyone is aligned on the shipping protocol. Miscommunication about plant sensitivity or handling instructions can lead to mishaps.”
“Regardless of what size business, mom-and-pop to large-scale operations, the key thing is to limit and minimize the exposure time to cold air as much as possible to avoid ending up with a plant popsicle,” says Jason Lamb, Shipping Manager at Pleasant View Gardens in Loudon, NH. “No one wants a plantsicle.”
Loading Docks
Loading plants on a cold day requires planning and following established procedures. A few minutes of sitting on a cold loading dock unprotected can be enough to damage sensitive plants. While some facilities are protected from the weather, others have to make do. Shipping plants in cold weather is what Lamb does, probably for more months of the year than he’d prefer.
“We try to move the plant material as late in the day as possible, so it’s as warm as it can be,” he explains. “When we’re going through the day pulling our material from greenhouse to greenhouse, we’re trying to let it warm up a little bit rather than do it first thing in the morning.”
Loading docks in New York can be chilly, and Opulgencia tells us her standard operating procedure.
“We’ve mitigated this by using a flushed loading dock. We also use heaters while loading and unloading trucks, ensuring that the plants don’t get exposed to cold temperatures during these transitions. This setup is crucial in preventing cold-sensitive plants from suffering any damage once they arrive or before they leave the facility.”
Problems at the Receiving End
While a grower can control their own procedures when loading a truck, conditions at the receiving facility might not be as suitable.
“Historically, from my experience, most problems seem to be unloading at the customer location,” Lamb says. It could be that the customer can’t get the truck close enough to the loading doors, or a few racks get left on the dock while the forklift runs back and forth. Maybe there’s some other hiccup. “You start adding in or layering in those little exceptions, and you don’t think much of it, but it all adds exposure time to that plant material.”
Cold exposure works in a cumulative manner, leaching heat out of the plant and increasing the likelihood of damage.
“How the plants are handled on arrival is a critical factor,” Opulgencia says. “When we receive shipments, we make it a priority to unpack the material right away. We triage the plants, prioritizing those that need immediate attention to ensure they acclimate to their optimal temperature.”
Third-Party Carriers
While some shipments go out on company-owned trucks, others are shipped via 3PL, or third-party logistics. Whether that’s FedEx or a private carrier, it’s a potential source of problems. Drivers may be making multiple stops, and each time the door opens is a chance for the temperature inside the truck to drop.
“We coach our own drivers as much as possible. However, the 3PL drivers we work with aren’t as vested as we would hope them to be. We’ve probably had a couple of shipments every year where a third-party logistic carrier exposes some material,” Lamb says. Without clear communication, they might not pay enough attention or assume that because the reefer unit is running, there won’t be a problem.
Temperature-Controlled Trucks
“What we see from everybody coming out of a warm climate going into a northern climate is they use reefers,” says AJ Lambert, Vice President of Sales and Account Management at Container Centralen. A reefer truck doesn’t just keep things cold; it controls the temperature inside the trailer, which allows growers to keep plants warm if needed. Most of them are capable of a range between subzero and about 77°F.
“We maintain a temperature of 55 to 65 degrees in the reefer trucks,” Lamb says. Opulgencia agrees, telling us all their loads heading into their New York location from Florida are brought in on reefer trucks.
Watch the Weather Forecast
The weather isn’t just a topic for small talk. Cold out there, eh? Watching the forecast on your plants’ route is critical, as is monitoring the weather at the destination.
“I’m monitoring the weather on a daily basis, sometimes hourly,” Lamb says. Depending on the predicted temperatures, he’ll hold up shipments if temperatures are predicted to be in the single digits or lower. Getting a good feel for what the weather is shaping up to be requires more than a snapshot look.
“Whether it’s here at our facility in New Hampshire or at the destination location, we’ll hold those shipments and either try to ship later in the week, if possible, or if the weather is not cooperating, we’ll roll those orders to the following week,” he tells us.
While that means a delay or inconvenience in holding a product that was scheduled to be gone, it’s better for the customer to get plants in good condition. As he said, no one likes a plantsicle. “There’s definitely been some weeks where we’ve gone a couple of weeks without shipping.”
Wrap the Racks and the Plants
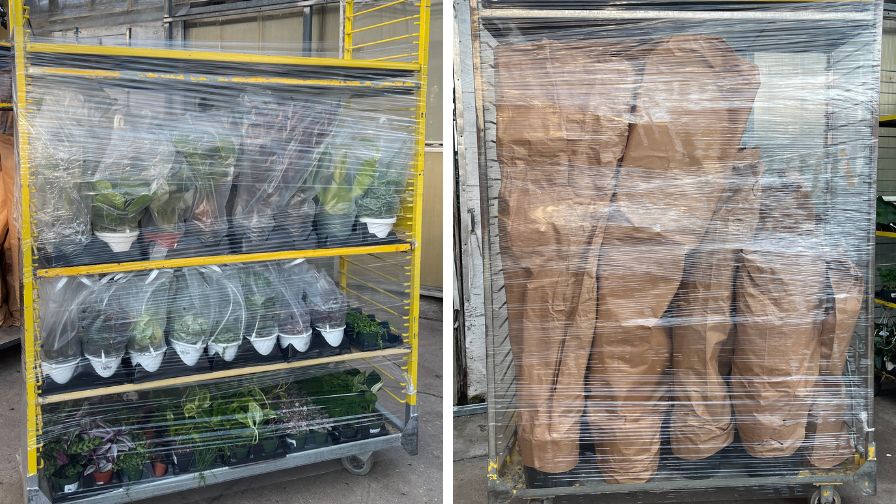
Plants and delivery racks carefully wrapped and ready for shipment. | Emma’s Garden Growers
While some winter plant shippers prefer wrapping the plants for the entire transit, others like to let them breathe and wrap them at the end before unloading. But they all agree that it is necessary.
“Nothing goes outside unless it has some sort of cover,” Lamb says. They have covers for the racks or blankets and wrapping material for smaller orders of a few flats or trays. The important part is to avoid the short burst of freezing temperatures on their way into and out of the truck.
Opulgencia likened their system to a plant burrito. “We wrap the carts in plastic, which not only keeps the cold air out but also traps the heat inside. This creates a mini greenhouse effect, minimizing cold damage, especially from freezing winds during transport. Plants that are especially sensitive to cold, like tropical varieties, benefit from being sleeved or even double-sleeved. This adds a protective layer that helps retain warmth during transit.” And then it’s in a heated truck. Sounds pretty cozy.
Training Staff
Remember, the individual who has been part of your team and working well on the loading dock for the last seven months may still not be familiar with cold-weather precautions. Training your staff is an essential element to safe winter plant shipping.
Lamb explains their philosophy, “We coach it as much as we can during our onboarding process and as the new hires are getting acclimated. Probably the biggest ones would be our drivers. Again, just constant reminding. Keep an eye on the temperatures. If something’s extremely cold and you’re not sure how to handle it, definitely call back to the office and get some direction.”